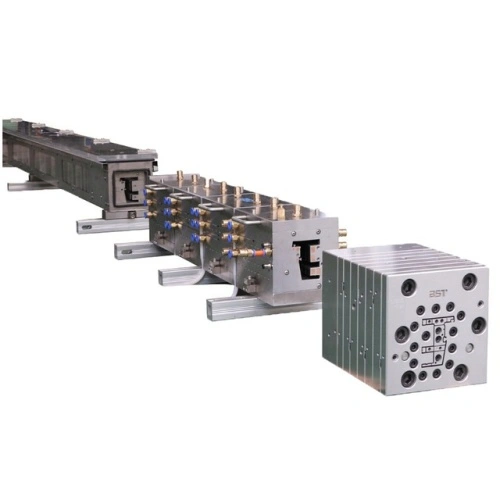
Plastic Extrusion Mold Manufacturing
When designing plastic extrusion molds, the following steps can be followed:
-
Needs Analysis: The first step is to determine the requirements for the plastic part to be produced. This includes factors such as dimensions, material properties, tolerances, and the production process.
-
Material Selection: Choosing the mold material is crucial. Typically, steel or aluminum is used. The material should be evaluated for durability, thermal conductivity, and cost.
-
Mold Design: Mold design is based on the shape and dimensions of the part. CAD (Computer-Aided Design) software is used during this phase. Internal cavities, cooling channels, cores, and ejection points are designed.
-
Cooling Channels: In plastic extrusion molds, cooling channels ensure rapid and uniform cooling of the plastic part. This extends the mold's lifespan and reduces production time.
-
Core Design: The core shapes the internal surface of the plastic part. A well-designed core affects the quality of the part.
-
Ejection Points: Points where the plastic part will exit the mold must be designed. The placement of these points depends on the part's shape and the production process.
-
Assembly and Part Functions: Mold assembly and part functions should be considered to facilitate the mold's use.
-
Prototype Production and Testing: After the design is completed, a prototype should be produced and tested. This is important for identifying design errors.
Plastic extrusion molds can vary based on the characteristics of the plastic part to be produced and the production process. Collaborating with a professional mold designer or engineer ensures the best results.