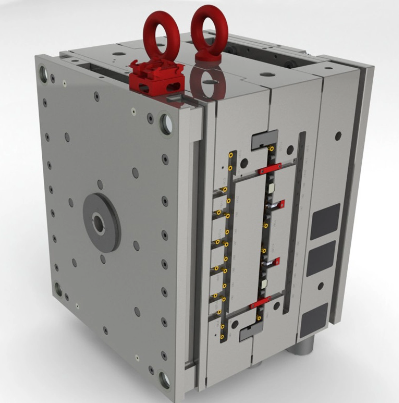
Plastic Injection Mold Design Considerations
Several important factors must be considered when designing plastic injection molds. Here are some key points to keep in mind during the design phase:
-
Part Design:
- The first step is to design the plastic part to be produced. The part’s dimensions, shape, tolerances, and requirements are determined at this stage.
- The purpose and function of the part influence the design process. For example, an automotive part may have different requirements compared to a medical device part, which may require more precise design.
-
Material Selection:
- The choice of plastic material depends on the part’s intended use and environmental factors. Considerations include mechanical strength, chemical resistance, and temperature tolerance.
-
Mold Design:
- Mold design determines the shape and dimensions of the part. The mold consists of two halves: the upper half (cavity) and the lower half (core).
- Cooling channels, ejection points, and tolerances should be considered in the mold design.
-
Flow Simulation:
- Flow simulations can be performed using computer-aided design (CAD) software. This shows how the plastic will flow within the mold.
- Design improvements can be made based on simulation results.
-
Material Flow and Filling Analysis:
- The flow of material and how the part fills should be analyzed during mold design.
- Filling analysis is important to prevent air traps and material buildup.
-
Mold Material:
- The material used for the mold affects the durability and longevity of the plastic injection mold. Typically, steel or alloy steel is used.
-
Details and Surface Finish:
- The mold surface determines the surface quality of the part. A good surface finish affects the appearance and performance of the final product.
Plastic injection mold design is a complex process and should be carried out by experienced engineers. At this point, our professional designers and engineers are dedicated to providing our clients with top-notch service.